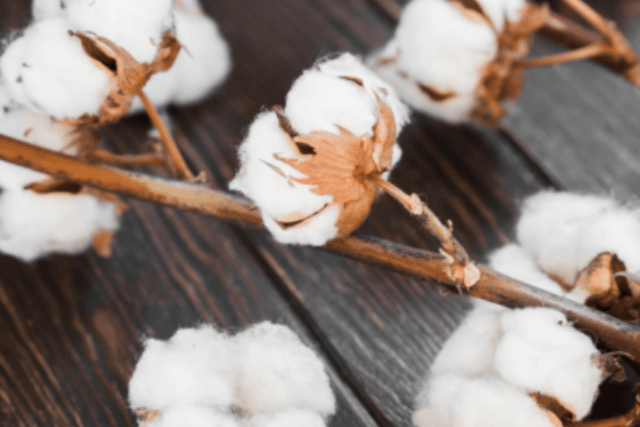
Untangling the Cotton Supply Chain
Cotton Ginning
After that, the cotton is sold to ginning mills, where the seed and bale of the raw cotton are separated. There are three results from the ginning process:
Seeds : About 55% of the seed cotton’s weight is made up of cotton seeds. They are very valuable and are used to plant the next crop, as well as in oil, plastics, stock feed, cosmetics, and margarine.
Lint : Lint accounts for about 35% of seed cotton’s weight. After the lint has been separated, it is compacted into bales so that it can be transported easily.
Waste : The remaining 10% of seed cotton is considered trash or waste. Waste cotton fiber can be used to make ethanol or make products that clean up oil spills. Additionally, it can be used as fertilizer
Cotton Yarn Spinning
The yarn is placed on the spinning frame’s rings and allowed to pass through a number of sets of rollers that are rotating at progressively higher speeds.
As the final stage of yarn spinning, the draft, twist, and winding of the yarn are all completed in one operation. The yarn is rolled by the rollers and wound up on the bobbins.
After that, the ring frames are removed and the yarn-filled bobbins are used for bleaching, weaving, and other processing.
Cotton Weaving
In order to weave the desired fabric, the warp thread and weft yarn are crossed over one another in a
predetermined manner. A loom is a machine that was made to do this job. Before the warp and weft yarns can be inserted into the loom, they are first prepared. Handlooms and power looms are the most common types of looms. The fabrics are then finished and sold to customers.
We are actively altering India’s natural fibers supply chain by collaborating with all genuine industry stakeholders. In order to improve the supply chain,
we conduct expert interventions at each stage. Being one of the Leading sourcing units we export high quality raw cotton to over 10+ countries.